What is Construction Safety Management?
The construction industry poses significant health and safety risks to site workers due to their working at heights, heavy machinery, adverse weather conditions, and frequent occupational hazards, resulting in serious injuries, financial losses, and damage to damage to the reputation of the company or builder.
Construction Safety Management involves systematically identifying, preventing, and managing risk within the construction sites to ensure the health and safety of workers, the public, and the environment. It encompasses various practices, policies, and procedures to create a safe working environment and prevent workers from accidents or injuries.
Major Hazards in Construction Industries
- Materials or tools falling from Heights
- Chemical Exposure & spills
- Falls from a height without proper protection
- Breathing Dust from construction materials
- Vehicle & Heavy Machinery mishaps
- Working in Confined Spaces
- Slips, trips & falls from uneven surfaces
- Fire Explosion
- Working at Electricity
Importance of Construction Safety Management in workplace
According to the U.S. Bureau of Labor Statistics (BLS),
- The construction industry consistently faces 1,102 fatal occupational injuries every year.
- Falls, struck by objects, and electrocution incidents accounted for approximately 63.7% of construction worker deaths.
As per the National Safety Council (NSC),
- The average cost of a non-fatal injury in the construction industry can range from $41,000 to $82,000 per incident, considering medical expenses, compensation, and indirect costs.
The above statistics highlight the ongoing challenges and the critical need for robust safety management practices in the construction industry. It is important to implement proper safety management system at the workplace to minimize the production delays, financial risks and maximize the company’s reputation, employee morale, and attract more skilled workers.
Risk Management System at Construction
PDCA (Plan-Do-Check-Act) is a four-step risk management method used for the continuous improvement of various organizations, including construction safety.
- Plan: Evaluate the workplace, identify hazards, and plan policies and procedures as per the risk assessment report
- Do: Implement the safety policies & procedures as per the plan
- Check: Regularly review and assess the safety procedures and its effectiveness
- Act: Update changes, improve the remedial measures based on assessment and take corrective action when needed.
How to Improve Safety Management at Construction site?
Each construction site has unique challenges. Appointing dedicated safety officers at your workplace ensures focused oversight, tailored solutions, and continuous monitoring to mitigate risks effectively. They take specialized attention and proactive measures to elevate safety management, reduce hazards, cultivate a culture of safety consciousness among workers, and significantly improve your worksite safety.
Role of Safety Officers at Construction Sites
- Safety officers will conduct thorough risk assessments on workplace to determine potential hazards and create safety regulations and policies to overcome them.
- They will verify the tools and equipment are of good quality, specify adequate personal protective equipment for workers, and guide them on handling it properly.
- They will find the best way to keep workers safe from fire explosion, chemical spills and avoid falls and injuries when working at heights.
- They regularly carry out mock drills on managing emergencies and test the effectiveness of site emergency response plans.
- They will investigate accidents, gather evidence to determine their causes, and document their findings to prevent future accidents.
- They will continuously monitor all the safety-related documents, reports, and issues and keep them updated.
Benefits of Equipping Your Workers with Construction Safety
- It minimizes the risk of accidents, injuries or fatalities among workers and boosts Employee confidence for better job performance.
- They will acquire knowledge to identify workplace hazards, know the safety precautions when working with different hazards, and respond to all industrial warning indicators.
- Training makes them familiar with work at height protection, safety in excavations, scaffolding safety, electrical safety, material handling safety, welding and gas cutting safety, and construction safety management.
10 Golden Safety Tips to follow in construction Safety
- PPE: Use appropriate PPE while performing work.
- Work Permit: Obtain the necessary permit before entering into the work
- Work at height: Implement fall protection measures while working at heights
- Confined space entry: Follow the safety procedures for safe entry and work in a confined space
- LOTO Safety: Ensure proper lockout/tagout procedures for machinery maintenance.
- Lifting operation: Conduct lifting operations with proper precautions and equipment.
- Safety Device: Never bypass or disable safety devices on equipment.
- Safe driving: Practice safe driving on-site and follow the speed limits.
- Barricades: Install barricades when working under loads or overhead structures
- Accident Reporting: Immediately report accidents and carry out thorough investigations.
Employee Safety is a strong foundation for a thriving construction industry, so empower your employee with our safety training & ensure safety compliance.
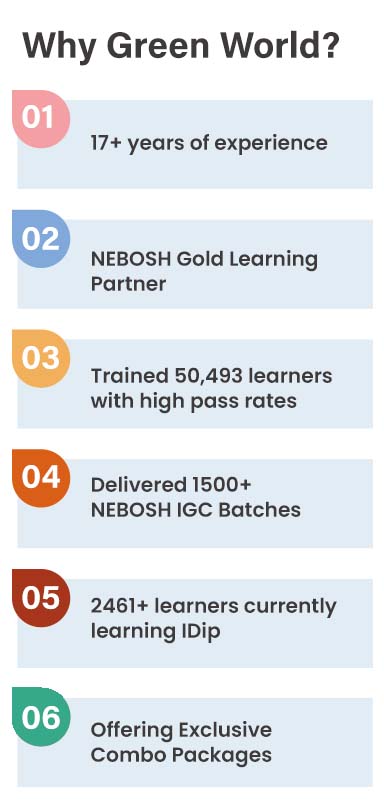