Among the various hazards in the industry, vibration is an occupational hazard that is very widespread for employees. It is present in wide-ranging sectors such as construction, energy, manufacturing, etc. When a worker or an operator is in contact with the surface of a machine that is vibrating, the mechanical vibrations are transmitted directly to the body. This affects the individual tissues or even the entire body. The vibration affecting humans is termed human vibration, which is further subdivided into hand-arm vibration (HAV) or whole-body vibration (WBV). Human exposure to vibration remains a significant risk factor which is associated with neural, vascular, and musculoskeletal disorders in the body. Vibration-induced injuries cause significant organizational costs, including much pain and suffering for the worker/operator.
HAV exposure at work arises from using hand-held tools/equipment, hand-guided machinery and hand-fed machines. Hand-arm vibration occurs when one or both upper limbs are in contact with a vibrating surface. Examples of machines where workers may encounter hand-arm vibration are grinders, hammer drills, lawnmowers, plate compactors, pedestal grinders, forge hammers, etc.
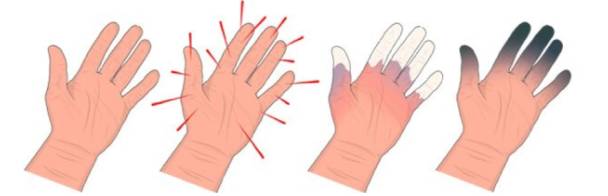
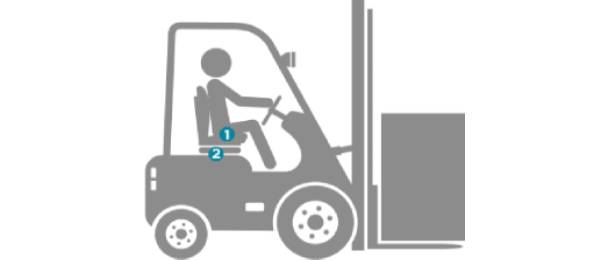
On the other hand, WBV can occur when the body is supported on a surface that is in vibration. Workers typically experience WBV either when working near heavy vibrating industrial machinery or when operating various forms of transport vehicles. The vibration passes through the supporting surface the worker is in contact with, such as the floor upon which the heavy vibrational industrial machinery is operating or a poorly adjusted seat when driving bulldozers, tractors, lorries, excavators, etc., across rough terrain.
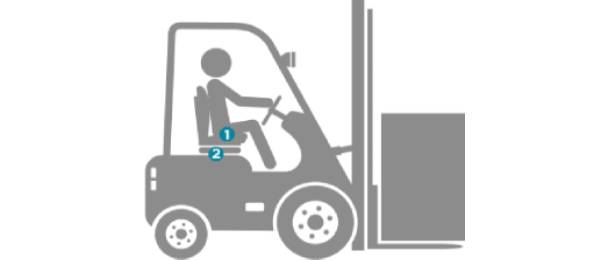
Regular and frequent exposure to this vibration, usually over many months or years, can affect the operator’s health. Ill-health effects and changes in the human body that result from contact with mechanical vibrations are recognized as an occupational disease which is called “vibration syndrome” (or “vibration disease”).
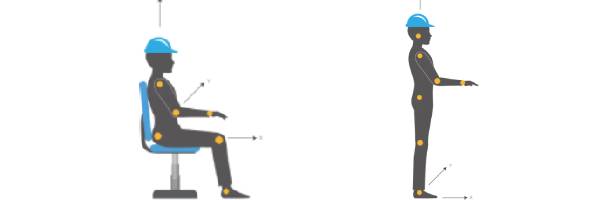
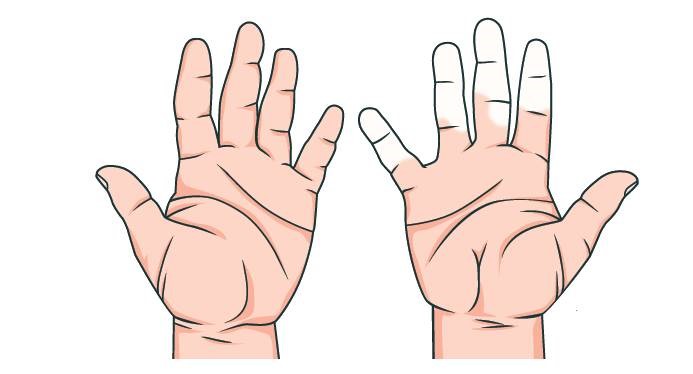
HAV can cause various pathological changes in the vascular (cardiovascular), nervous, and osteoarticular system. In addition, it causes a form of vascular disorder characterized by low blood circulation in the fingers. Symptoms manifest by the fading of one or more fingers’ fingertips, commonly termed as “white finger diseased” or “vibration white finger (VWF)”. VWF is known to cause a feeling of numbness or tingling in the fingers, often accompanied by blanching (or whitening) of the fingertips. When VWF occurs, the fingers may appear drained of blood and become white. These symptoms can last anywhere from a couple of minutes to several hours.
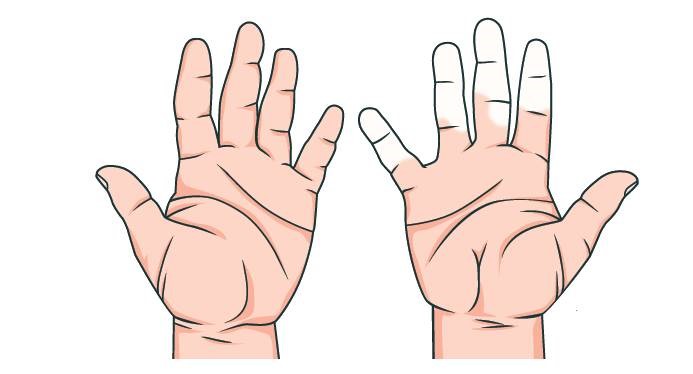
Other common symptoms include a feeling of numbness in the fingers, tingling sensation in the hands and fingers, loss of harm or arm strength, general difficulty picking up small or medium-sized objects, general pain in the thumbs when trying to grip an object, and a feeling of weakness in the hand muscles. Over a period of time, exposure to HAV affects the bones, muscles, joints, and nervous system, causing a condition collectively known as hand-arm vibration syndrome (HAVS). In addition, HAV is also known to cause carpel tunnel syndrome (CTS) and nerve damage.
Further, workers can experience sleep disturbance and distress, reduced ability to work in cold and damp conditions (generally outdoors), which may trigger painful, finger-blanching attacks, and an inability to do fine work (such as assembling small/tiny components) or completing simple everyday tasks such as buttoning the shirt. The risk of developing HAVS increases with the intensity and duration of exposure to vibration. Continued exposure results in worsening HAVS symptoms. Many workers need to be more familiar with the potential seriousness of hand-arm vibration syndrome. It must be noted that medicine cannot cure white finger disease, so treatment of HAVS is symptomatic. Thus the only effective way to avoid vibration disease is through prevention.
The vibration which is transmitted through the seat or feet (known as whole-body vibration or WBV) is experienced by drivers of specific mobile industrial machinery. Other work factors, such as poor posture and poorly adjusted seats, can contribute to the outcome of WBV.
Exposure to whole-body vibration (WBV) causes back pain (especially in the lower back area),damage to the spinal discs, and damage to the spinal vertebrae, creating an onset of osteoarthritis. Spinal degeneration is likely to be one of the deleterious outcomes of exposure to WBV. Most exposure to WBV at work is unlikely on its own to cause back pain. However, it may pose a risk when there is unusually high vibration or jolting, or the vibration is uncomfortable for a long time on most working days. Usually, in such situations, the risk from
WBV is related to the overall time the operator or driver is exposed to the vibration and the number of shocks and jolts they experience each day. Moreover, in some cases, WBV may aggravate a back problem caused by another activity, e.g. a muscle strain caused by an
accident when lifting a heavy object or during physical activity such as sport.
When workers are exposed to the risk of vibration in the workplace, it stands as the legal duty of the employer to make a suitable and sufficient risk assessment. They must identify the specific control measures that are needed to reduce the risk of vibration. The employer should daily assess the exposure to vibration by means of observation of specific working practices, including making references to relevant information on the probable magnitude of vibration corresponding to the equipment used in the particular working conditions. If deemed necessary, the employer may measure the magnitude of vibration to which the employees are liable to be exposed to. Such assessment shall enable the employers to determine whether the employees are likely to be exposed to vibration at or above an exposure action value or above an exposure limit value.
It is pertinent to note that a vibration-specific risk assessment should generally include the consideration of the magnitude, type and duration of exposure, including any exposure to intermittent vibration or repeated shocks; the effects of exposure to vibration on employees whose health is at particular risk from such exposure; any effects of vibration on the workplace and work equipment, including the proper handling of controls, the reading of indicators, the stability of structures and the security of joints; any information provided by the equipment manufacturer; availability of any other replacement equipment which is designed to reduce exposure to vibration; any extension of exposure at the workplace to WBV beyond normal working hours, including exposure in rest facilities supervised by the employer; specific working conditions (such as low/cold temperatures; and any appropriate information obtained from health surveillance including, where possible, published information.
Such a risk assessment should be reviewed by the employer on a regular basis, including when there is any reason to suspect that the risk assessment may be no longer valid or there have been significant changes in the work to which the assessment relates. As a result of the
review, the employer should make specific changes to the vibration risk assessment.
Employers need to be aware of vibration exposure limit values and action values as stated in their respective applicable health and safety legislation. For example, in the United Kingdom, the statutory legislation regarding vibration is The Control of Vibration at Work Regulations 2005. This piece of legislation states the exposure limit values and action values for HAV and WBV.
For HAV:
Daily exposure limit value is 5 m/s2 A(8)
Daily exposure action value is 2.5 m/s2 A(8)
For WBV:
Daily exposure limit value is 1.15 m/s2 A(8)
Daily exposure action value is 0.5 m/s2 A(8)
The daily exposure limit value (ELV) is defined as the maximum amount of vibration which a worker/employee may be exposed to on any single day.
The daily exposure action value (EAV) is defined as the level of daily exposure to vibration at or above which you are required to take certain actions to reduce exposure.
In order to assess the daily exposure to vibration of an employee/worker, it is necessary to know which specific tasks expose employees to vibration, the type of tools/equipment they use, the purpose for which these tools/equipment are used, and the total time the worker/employee is in contact with the tool/equipment whilst it is operating.
Employers can make use of a variety of possible sources of suitable information on vibration magnitudes for their risk assessment. These would include the equipment manufacturer’s manual for declared vibration emission values, additional information from the equipment
supplier, vibration consultancies, enforcement agency websites, research organizations, trade associations and from vibration measurements made in the workplace.
Vibration measurements can be made through the use of vibration level meters which are also called vibration dose meters, that are equipped with vibration acceleration sensors.
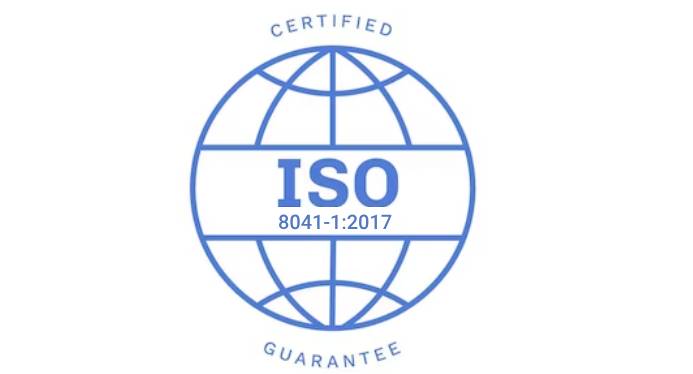
The ISO standard ISO 8041-1:2017 Human response to vibration – Measuring instrumentation – Part 1:
General purpose vibration meters help in the selection process by defining the parameters of a human vibration meter. Nowadays, accelerometers based on MEMS technology (Micro Electro-Mechanical Systems) are more commonly used to measure vibration. The small size of the MEMS technology sensors allows it to be attached to human hands without creating any distraction to the performance of everyday activities. These sensors can even be placed underneath anti-vibration gloves.
The Ways in Which Employers can Reduce the Risk of Vibration Exposure to their Employees are as Follows:
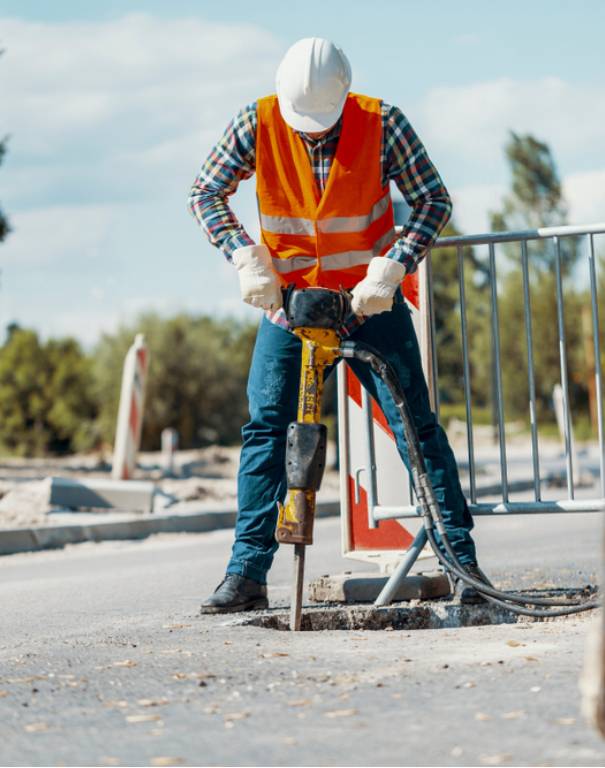
- Implementing other working methods which eliminate or reduce exposure to vibration.
- Selecting work equipment of appropriate ergonomic design, which produces the least possible vibration.
- Providing auxiliary equipment which can reduce the risk of injuries caused by the vibration.
- Implementing appropriate maintenance programmes for the work equipment and systems.
- Evaluating the design and layout of workplaces, workstations, and rest facilities.
- Providing information and training for employees that is suitable and sufficient in order that work equipment may be used safely and correctly, thus minimizing exposure to vibration.
- Limiting the duration and magnitude of exposure to vibration.
- Creating appropriate work schedules that include adequate rest periods.
- Providing clothing to protect employees from cold and dampness.
- In addition to the above, the employer shall provide health surveillance to prevent or diagnose any health effects linked with exposure to vibration.
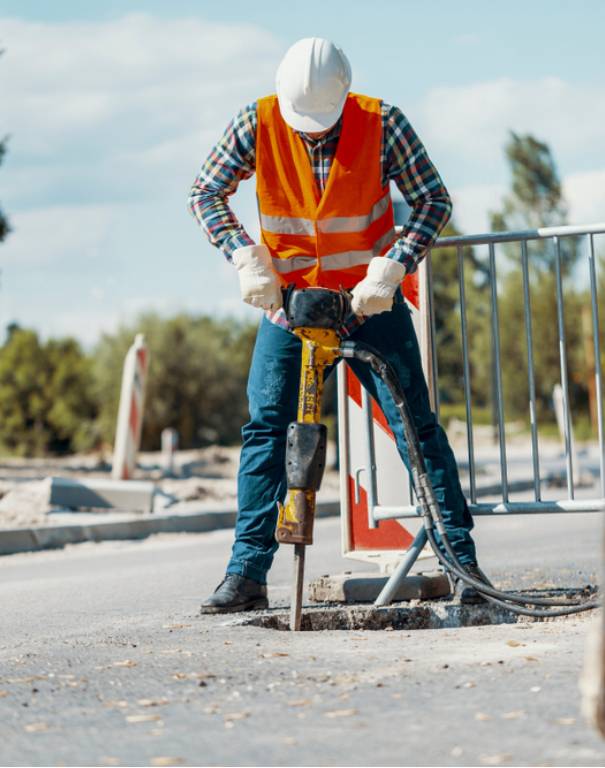
Contact Us
Kindly call our Experts @ +91 8121563728 / +91 8015527650 or mail us @ kalyan.r@greenworldsafety.com / indumanasa.m@greenwgroup.com
Get Your Query Answered / Get Expert Assistance To Choose the Right Course for You Or Your Associates